Oil Tank Corrosion: A Major Source of Equipment Failures
Oil tank corrosion is a major source of expensive equipment failures and reduced operational functionality – and is one of the most common issues we respond to here at Crown Oil.
Steel tanks are regularly used to store bulk fuel thanks to their superior characteristics when compared to plastic tanks. They are more robust, can withstand larger impact and are non-porous, meaning they don’t absorb any of the stored fuel.
But unfortunately, despite their strengths, steel tanks are also more vulnerable to corrosion from the elements, such as UV light, heat and condensation.
Over time, corrosion decreases a tank’s integrity and eventually penetrates the tank structure, initiating tank bottom perforation. This can cause oil to leak into the environment which can result in huge clean-up costs.
Tank owners have a legal duty to ensure your stored fuel is safe and secure, without posing a risk to the environment.
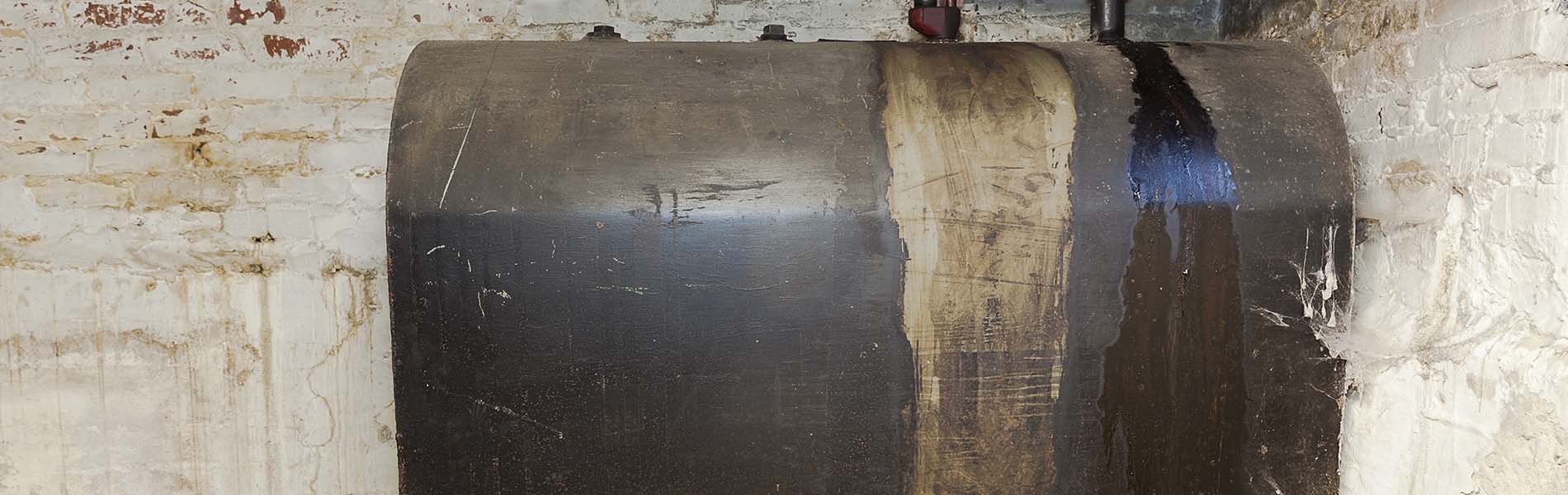
So what exactly causes corrosion and how you can help avoid it?
Water
Unfortunately, during spring and summer, water can form inside of a steel tank due to heat gain and evaporation. This causes the tank to breathe and results in water and microbial contamination.
As corrosion forms from the inside of an oil tank, the extent of a problem is usually not known until external problems have developed which by this point, are often too late to fix.
Corrosion types
- General corrosion – occurs throughout a tank
- Local corrosion – appears in specific areas where water collects or flows
- Pitting corrosion – found along horizontal surfaces, the bottom of tanks and where water accumulates. Once it becomes thicker than 1/3 of the wall depth, it becomes a big problem
- Weld metal corrosion – transpires when welding metal interacts with metal in the tank, causing an electrolytic reaction
Sludge
Oil tank corrosion, algae and sludge build-up are responsible for 62% of equipment failure.
When a tank becomes corroded, the oxidation of hydrocarbon ingredients is increased which causes sludge, bacteria and fungi to accumulate, reducing the quality of the stored fuel.
Corrosion on the bottom of a tank reduces fuel lubrication and clogs filters, whereas in the upper filter spaces, it can hinder the operation of release detection and eventually lead to equipment failure.
Modern fuel
Fuel tanks also face several challenges due to the nature of the fuels stored, and diesel tank corrosion is particularly common.
The introduction of ultra low sulphur diesel (ULSD) and an increase in bio content and modern refining techniques means that the risk of contamination and general corrosion or pitting is now greater than ever.
Although some corrosion is unavoidable, there are numerous services and products that can help fight it. These must form part of your planned preventative maintenance programme (PPM) and will help you avoid high cost and downtime implications.
Tank corrosion protection
Fuel testing
In 2018, we were called out to 482 instances of corrosion – where the majority could have been avoided by regular checks, tank maintenance and keeping tanks full to avoid the risk of moisture.
Generally, diesel should not be stored for longer than six months without regular checks by a professional company. Regular fuel testing will detect contamination and corrosion early on so that any faults can be sourced, diagnosed and repaired.
Fuel testing looks at water, FAME and sulphur content, viscosity, density and the amount of microbial contamination within fuel. If left untreated, it can cause havoc in machinery’s internal components, bringing operations to halt or damaging it beyond repair.
Internal testing is the only way to truly determine the health of your tank. This involves specialist cleaning techniques such as confined space entry (man entry) cleaning by a qualified team.
The tank must be first emptied of any contents and then a complete internal clean down can follow, using pressure jetting to eradicate any loose metal exposing any pitted or rusted areas.
The engineers must then carry out non-destructive testing (NDT) to test the metal thickness at various points in the tank. This process looks explicitly at the base plate as it’s not noticeable until the tank is cleaned. Fuel tank thickness usually varies from 6-12mm depending on the size of the tank or site specification. If the tank thickness has reduced by more than 20% once tested, action must be taken.
Pipework must also be checked as frequently as tanks using pressure testing and NDT if the pipework is above groundwork and clearly visible.
Double skinned tanks
A high-performing liner, such as a single or double skin, offers leak detection and acts as a safety net, providing excellent ROI.
A double skin provides twice as much protection and ensures the original tank is contained within a vacuum which helps prevent corrosion as there’s no moisture or air within. The thicker the skin, the better the protection.
Keep tanks full
Water encourages corrosion in the top half of the tank. Keeping tanks topped up, particularly during spring and summer, leaves less space for air, humidity and therefore less condensation.
Paint coating
Using a coating solution from the outset, such as Hammerite Direct and Rust Metal Paint will protect your tank for much longer and help prevent corrosion. Its corrosion-resistant finish reduces surface damage by repelling water and preventing rust from forming underneath.
Secondary containment
A bund, also known as secondary containment, is made from concrete or brick and is required by law to contain and prevent spills that can occur from tank penetration. The extra outer layer is designed to protect the inner tank and must be able to hold 110% of the fuel. If there’s a leak or breach of the inner tank, for example overfilling or water build-up, the outer bund has the capacity to contain it safely.
Outside bunds are exposed to natural elements so are less likely to become filled with rainwater. However, if rainwater does build up, it reduces the containment capacity and increases the risk of oil escaping the bund wall.
Tank dewatering
Tank dewatering at outlet pipes, for example using a bung, is essential to detect liquid interfaces between the oil and water. A bung must be fitted 0.25inches from the base of the tank to provide an outlet for water to escape and keep the oil contained.
Tanks must be dewatered every six months to prevent water building up and causing corrosion.
Fuel polishing
If a significant amount of sludge is found in a tank, you may benefit from filtering out contaminants on a regular basis. This involves filtering the contaminated fuel through a series of increasingly finer filters and gradually removing water, sediment and microbial contamination until it’s clean.
When fuel degrades in quality, its molecules join together to form new polymers which reduces the quality of the fuel. Our advanced depolymerising technology breaks down the particulates and polishes the fuel until it’s clean and optimised.
If you suspect problems of oil tank corrosion then it’s vital that you take a proactive approach and get in touch as soon as possible. That way, we can help you to solve the issue before it becomes too severe to be rectified. Call us today on 0330 123 1444 to learn more.
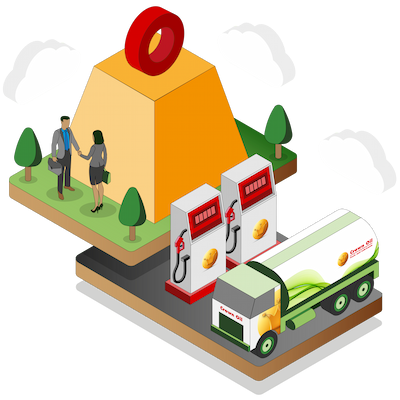